In traditional processes, the carbon content of magnesium carbon bricks is generally 14%-20%, and the source of carbon is basically from graphite. This is because graphite is resistant to high temperatures, has little mass loss, small volume expansion and contraction, and poor wettability to slag. Traditional magnesium carbon refractory materials will gradually expose the following problems during long-term use:
(1) Carbon is easily oxidized during high-temperature smelting. After oxidation, it is easy to form a porous structure in the refractory material, which reduces the strength of the material and makes the material easily corroded and penetrated by slag;
(2) High thermal conductivity increases the temperature of molten steel, takes away more heat energy, increases energy consumption, and causes the corrosion of refractory materials to worsen;
(3) High thermal conductivity causes the furnace shell and metallurgical containers to deform or damage;
(4) It consumes a large amount of precious graphite resources and increases the emissions of CO2 and CO;
(5) When used as a lining material for VOD refining furnaces and other special converters, it will increase the carbon content of molten steel and fail to meet the smelting standards of low-carbon clean steel.
Therefore, reducing the amount of carbon used and preparing low-carbon magnesium-carbon refractory materials has become an inevitable trend in research. The carbon content of low-carbon magnesium-carbon bricks currently under study is generally not higher than 8%, because as the carbon content decreases, the thermal conductivity of magnesium-carbon bricks will decrease, the elastic modulus will increase, and the thermal shock stability will decrease. Compared with high-carbon magnesium-carbon bricks, when the carbon content decreases, the slag will penetrate into the pores of the bricks, resulting in the deterioration of the slag and corrosion resistance of magnesium-carbon bricks. How to reduce the amount of graphite used while maintaining the superior performance of magnesium-carbon bricks so that they can occupy an unparalleled position in the steelmaking industry has become a hot issue that scholars at home and abroad are vying to study.
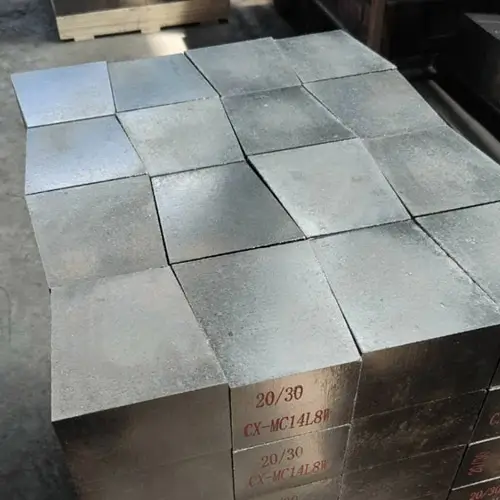
Low carbon magnesium carbon brick is a refractory material with excellent performance obtained by reducing the carbon content in magnesium carbon brick without changing the traditional preparation process. Since the amount of graphite in low carbon magnesium carbon brick is halved, the advantages of graphite such as high thermal conductivity, extremely small thermal expansion coefficient and elastic modulus cannot be brought into play, resulting in the deterioration of thermal stability and slag corrosion resistance of low carbon magnesium carbon brick. Therefore, how to reduce the thermal stability and slag corrosion resistance of low carbon magnesium carbon brick has become the key to research. We can control the matrix structure of magnesium carbon brick by looking for carbon raw materials with better performance, so as to achieve the purpose of improving the thermal stability and slag corrosion resistance of low carbon magnesium carbon brick. A good matrix structure requires appropriate carbon particles to control the composition, shape, size and distribution of pores in the sample: at the same time, a good matrix structure can greatly affect the thermal conductivity, thermal expansion coefficient and elastic modulus of the material, thereby improving the material’s oxidation resistance, thermal stability and slag corrosion resistance.
Some scholars use nanocarbon as a carbon source, add a small amount of nanocarbon in different proportions to graphite, and keep the total carbon content below half of the total carbon content in traditional magnesium-carbon refractory materials to prepare new magnesium-carbon refractory materials. Studies have shown that when 0.9% nanocarbon and 3% graphite are mixed, the performance of the refractory material reaches the best value. Because nanocarbon can be more evenly distributed in the matrix, it plays a role in filling the gaps between particles of different sizes of the starting material and the pores inside the nanocarbon, thereby reducing the apparent porosity of the refractory material and increasing the bulk density, strength, and corrosion resistance. In addition, nanocarbon can also reduce the stress caused by the volume expansion or contraction of the refractory material, thereby improving the uneven distribution of thermal stress inside the refractory material and improving thermal stability. The low-carbon magnesium-carbon bricks prepared by this method improve the performance of the refractory material while reducing the carbon content and improving the quality of the bricks.
Modified graphite was added to magnesia carbon bricks for ladle slag, and the effect of modified graphite on the various properties of magnesia carbon bricks was studied. The experimental results show that although the addition of 0-1% modified graphite will have an adverse effect on the volume density of magnesia carbon bricks, the volume expansion of modified graphite at high temperature can compensate for the matrix shrinkage of the bricks and fill the pores between the materials, thereby improving the slag resistance of magnesia carbon bricks. When 0.8% modified graphite is added, the gap between the aggregate and the matrix in the magnesia carbon brick is the smallest, and the slag resistance is the best.
Environmentally friendly coal pitch was used to replace graphite, and phenolic resin was used as a binder to prepare magnesia-carbon bricks after heat treatment at different temperatures, and various performance indicators of the samples were tested. Experimental results show that with the gradual addition of environmentally friendly asphalt, the bulk density of the sample decreases, the apparent porosity increases, and the linear change rate becomes smaller, but the compressive strength increases significantly. Through microstructural analysis, it was found that at high temperatures, fibrous AlN and nano-magnesia-aluminum spinel are produced in magnesia-carbon bricks, and the higher the temperature, the more conducive to the formation of this structure.
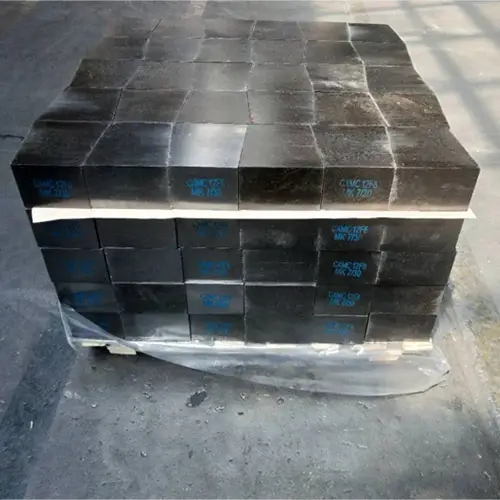