Due to the development of clean steel and ultra-low carbon steel and the requirements of energy saving, the development of low-carbon refractories has become an inevitable trend. At present, the main development trend of carbon-containing refractories used in various parts of the electric arc furnace, such as magnesium-carbon bricks, aluminum-carbon materials, Al2O3-MgO-C materials, or other carbon-containing unshaped materials, is the low-carbon and long-life. In recent years, with the development of the preparation process, the development of new binding agent and the development of nano carbon in refractory material technology, so that carbon refractory materials to low-carbon or even carbon free direction becomes possible.
It is well known that the main problem caused by the decrease of carbon content in carbonaceous refractories is the decrease of thermal shock resistance and slag resistance. Currently, the main ways to solve this problem include:
(1)Improve the thermal shock resistance of the material by improving the carbon structure of the binding carbon. The traditional binding agent of carbon-containing materials is mostly coal tar pitch or phenolic resin, and the carbon structure after carbonization of these binding agents is isotropic glassy, so it makes the material brittle, with high modulus of elasticity, which is unfavorable to the thermal stability of the material, and the material’s high-temperature strength is also low. After the introduction of graphitized carbon precursor or oxides with catalytic effect in coal tar pitch or phenolic acid resin, this modified binding agent can be carbonized into graphitized carbon under the environment of product use, or in situ formation of nano carbon fibers, through the improvement of the carbon structure and the formation of nano carbon fibers to improve the material’s thermal shock resistance and high temperature strength.
(2) Optimize the matrix structure of the material. In the case of a substantial reduction in carbon content, how to improve the contact ratio between aggregate particles and carbon particles, i.e., to reduce the scale of carbon particles and ensure that they are highly dispersed, is one of the important measures to improve the thermal shock resistance and slag permeability of low-carbon materials. Controlling the size, shape and distribution of pores by adjusting the particle size composition of matrix ingredients will also have a significant effect on the thermal conductivity of the material.
(3) Adoption of highly efficient antioxidants. With the reduction of carbon content in the material, anti-oxidation protection of carbon is particularly important, so the use of suitable high-efficiency antioxidants is also very necessary.
ABB type DC arc furnace anode used in the bottom of the conductive refractory material determines the life of the bottom electrode of the arc furnace, which is required to have good electrical conductivity, but also insulated from the furnace shell, and to ensure absolute safety. The most commonly used refractories are MgO-C bricks. MgO-C refractories require the following characteristics: low tincture rate, uniform and small by the influence of temperature, thermal conductivity is small, high temperature resistance to erosion performance, high temperature mechanical properties and good wear resistance. In order to meet the performance requirements, Japan’s earliest in this part of the MgO-C bricks with high carbon content, carbon content up to 25%. The domestic mostly used 18% carbon content of conductive MgO-C brick. In recent years, Japanese researchers have analyzed the residual bricks after electrode use, and found that the erosion and damage of MgO-C bricks are mainly caused by the cracking of brick seams during heating or cooling. It was thus proposed that the durability of electrode MgO-C bricks could be effectively improved by reducing the shrinkage gap of the bricks through appropriate residual expansion. Based on this, a new electrode MgO-C brick was developed, which is a magnesium carbon brick that maintains a low electrical resistance at both low and high temperatures, has a low thermal expansion and a high residual expansion (see Fig. 1). The performance of this new brick is very stable in use, which greatly improves the service life of the ABB-type furnace bottom electrode.
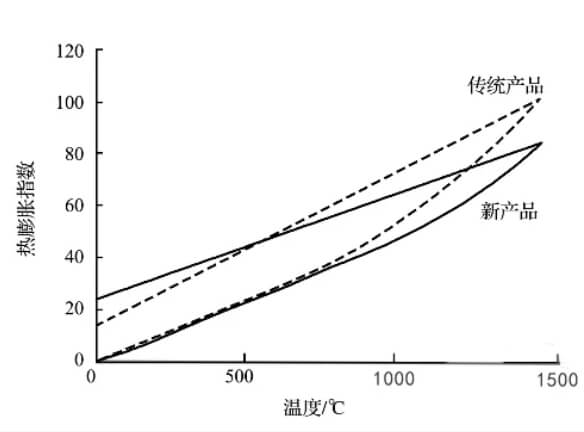
In the part of the furnace wall near the electrode is easy to form a “hot spot” high temperature area, will accelerate the erosion and destruction of the furnace wall bricks, resulting in localized melting, which is also a key part of the life of the furnace. The refractory materials used in this part are mainly asphalt combined with high purity magnesium bricks and magnesium carbon bricks, of which magnesium carbon bricks are the most widely used. Some studies have shown that the use of high-purity magnesium sand raw materials and the addition of metal powder to promote densification can effectively improve the erosion resistance of MgO-C bricks. Japanese researchers through the examination of electric furnace lining re-brick damage factors, found that at high temperatures to limit the diffusion rate of Mg vapor in the MgO-C brick can reduce the rate of brick damage. The slag erosion resistance test found that the erosion index of the bricks increased linearly as the apparent porosity of the MgO-C bricks (heat-treated at 1500°C) increased (see Fig. 2). Based on this, dense-structured MgO-C bricks (HIDEN) were prepared by reducing the metal powder and carbon content, adjusting the particle gradation and production process. The apparent porosity of HIDEN bricks and traditional MgO-C bricks is very close to that of traditional MgO-C bricks when the heat treatment temperature is ≤200°C, but the apparent porosity of HIDEN bricks is much lower than that of the traditional MgO-C bricks after the heat treatment at 1000~1500°C. The carbon content of the HIDEN bricks is 8%, which is only half of that of the traditional MgO-C bricks, but the HIDEN bricks have excellent resistance to spalling and erosion. The HIDEN bricks have excellent resistance to spalling and erosion. In addition, the application of anti-brittle coating on the working surface of HIDEN bricks, the bricks are applied to the working lining of the side wall of the electric arc furnace, and its service life is doubled compared with the traditional MgO-C bricks, which greatly improves the productivity of the electric furnace.
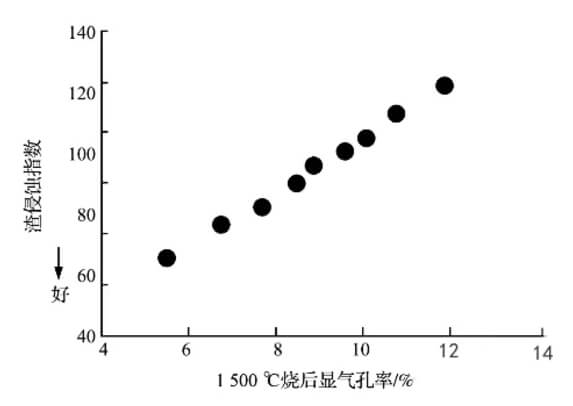
In addition, in view of the fact that castables have been widely used in ladle linings, but there is the problem of not easy construction when used for electric furnace linings, Japanese researchers developed a no-bake Al2O3-MgO brick with the same composition as that of the Al2O3-MgO castables, the basic properties of which are listed in Table 1, which can be used in place of the traditional MgO-C brick for the side walls of electric furnaces. Compared with MgO-C bricks, this new type of no-burn bricks has higher room temperature strength and lower thermal conductivity, and has good energy-saving effect.
Due to the wide application of water-cooling technology on the walls and lids of electric arc furnaces, seepage of water or water vapor can cause hydration of MgO or magnesium-calcium materials, which can lead to material damage, and oil-impregnated magnesium bricks, asphalt-impregnated magnesium bricks, or magnesium-calcium materials have become a feasible measure for preventing hydration. Japan developed modified MgO brick (Table 2), has excellent resistance to hydration, by autoclave (0.3MPa, 3h) hydration test, the new MgO brick weight gain rate of only 0.1%, while the traditional MgO brick weight gain rate of 5.4%. The application of this new MgO brick in the permanent lining of electric furnace can effectively avoid the hydration phenomenon caused by water seepage or cooling system leakage during the lining repair, which greatly prolongs the working life of the lining, reduces the number of repairs and replacement of the permanent lining, and effectively saves the cost of steelmaking.
The use of eccentric bottom outlet (EBT) is gradually increasing due to the expansion of water cooling area, reduction of refractory cost and reduction of slag discharge from ladle.EBT outlet is generally made of EBT tube with MgO-C brick masonry around its periphery, which needs to be replaced and repaired because of erosion and larger diameter with repeated steel output, which affects the productivity of the furnace. If the service life is prolonged by increasing the thickness of the EBT tube wall, the efficiency of the steel discharge will be low at an early stage due to the small diameter inside the tube. In order to control the initial diameter of the outlet EBT tube constant and make the outlet durable enough, the Japanese researchers compared the performance of three kinds of dense bricks by test (see Table 3), and found that compared with dense MgO-C bricks, Al2O3-MgO-C bricks not only have low carbon content, but also have better abrasion and erosion resistance, and finally selected Al2O3-MgO-C material as the main material to prepare the EBT tubes as the main material. The initial pore diameter of the prepared EBT tube can be further enlarged, and the steel discharge time is shortened and the operation efficiency is greatly improved after it is applied to the steel outlet of the electric furnace.