In the powder metallurgy furnace lining refractory material selection, its refractory materials have many categories, mainly heavy refractory bricks, including refractory clay bricks, high alumina bricks, silica bricks, fused corundum bricks, silicon carbide bricks, carbon bricks and so on.
1.Clay Brick
Clay brick is composed of refractory clay or kaolin (mainly composed of Al2O3, SiO2, H2O, and containing 6%~7% of metal oxides such as K2O, NaO, CaO, MgO, TiO2, Fe2O3, etc.). Clay brick is a soft clay (binding agent) and cooked clay mixed molding, sintered at 1300 ~ 1400 ℃ into products. Clay brick contains 30% ~ 40% of the Al2O3, the rest for the SiO2. clay brick is a weak alkaline refractory materials, can resist the erosion of acidic slag, but the alkaline slag corrosion resistance is poor, resistance to rapid cooling and heating is very good; Load softening temperature of 125-300 ℃, refractoriness 1610-1750 ℃, the highest operating temperature of 1300-1400 ℃. Clay bricks can be used to masonry furnace wall, roof, bottom, combustion chamber and other places. However, it has corrosive effect on Fe-Cr-Al resistance wire and should not be used as its shelving brick, and it is easy to be damaged by the erosion of CO and H2 in the controlled atmosphere.
2.High Aluminum Brick
High alumina bricks are refractory materials with Al2O3 content above 48%, which are made of high alumina bauxite (Al2O3-SiO2) as raw material and fired at about 1500°C. The refractoriness of high alumina bricks is 1750~1790°C, but the resistance to chemical attack is better. The refractoriness of high alumina brick is 1750~1790℃, and the load softening start temperature is 1420~1500℃, with better resistance to chemical erosion, but poor resistance to rapid cooling and heating. High-alumina brick re-firing shrinkage is generally larger, which is especially important to pay attention to for high aluminum bricks containing 60%~75% Al2O3. In the use of high alumina muffle furnace tube with insufficient firing temperature or use this high alumina brick masonry furnace roof, due to the large re-fired shrinkage, high temperature use for a period of time, it is easy to cause the top of the sinking or collapsing.
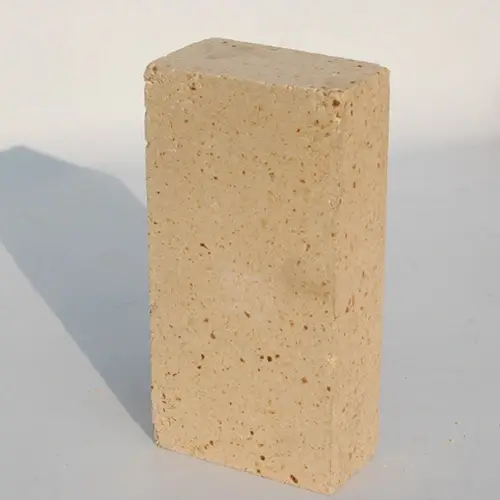
3.Corundum Brick
Corundum brick is a high-grade refractory material with Al2O3 content greater than 98%. According to the different raw materials used, corundum bricks are divided into two kinds: electrofused corundum bricks and alumina corundum bricks. Corundum has natural and artificial. Artificial corundum generally with industrial alumina (mainly γ-Al2O3) after high-temperature calcination and the formation of, but also by the non-crystalline alumina raw materials after high-temperature furnace melting made, often called electrofusion corundum.
Electrofused corundum is electrofused corundum sand as the main raw material, and add an appropriate amount of aluminum phosphate solution as a binder made of refractory products, the molding method of pounding (or machine pressure) molding method and gypsum mold casting method. Its firing temperature of 1700 ~ 1800 ℃, refractoriness of 1950 ℃, the beginning of the load softening temperature of 1770 ℃, resistance to rapid cooling and heating for 50 times, the density of 3.1 ~ 3.4g/cm3, the use of temperature of 1800 ~ 1850 ℃. Due to the corundum products good resistance to rapid cooling and heating, hardness, wear resistance, can be used as high-temperature molybdenum wire furnace furnace tube. It is worth noting that corundum products require high firing temperature, if the firing temperature is low, the same fusion is easy to produce heavy burning contraction, abrasion resistance will be reduced, resistance to acute cold and acute heat will be worse, this point is very important for the horizontal continuous molybdenum wire furnace furnace tube. Alumina corundum brick is the use of industrial pure alumina powder to add the appropriate amount of oxide (titanium oxide, chromium oxide, etc.) at 1600 ℃ above the firing, or more than 98% of alumina firing of pure alumina products. Such products are used at a temperature of 1750-1850 ℃, generally used as a high-temperature kiln, furnace lining, stove pipe, etc.
4.Silica Brick
Silicon bricks are oxidized siliceous refractories containing more than 93% SiO2, which are made of crushed quartzite with lime milk or other binder. Silica brick belongs to acidic refractory material, strong resistance to acidic slag, weak resistance to alkaline slag, use should pay attention to this point. Silicon brick refractoriness up to 1710 ~ 1730 ℃, load softening start temperature is almost close to its refractoriness, generally in 1620 ~ 1640 ℃ above, which is the biggest advantage of silicon brick; its disadvantage is the resistance to acute cold and acute heat is poor, and is sometimes used to masonry heating furnace high temperature part, but the intermittent furnace should not be used.
5.Magnesium bricks and magnesium-aluminum bricks
Magnesium brick is made of calcined magnesite (MgCO3) as raw material, which contains more than 80% magnesium oxide. Magnesium brick belongs to the alkaline refractory materials, good resistance to alkali corrosion, good erosion of iron oxide, refractoriness of up to 2000 ℃, the beginning of the load softening temperature of 1550 ~ 1600 ℃, in the high temperature for long-term use of the volume of a slight contraction, resistance to rapid cold and heat is not good, water-cooling is only 3 ~ 5 times. Magnesium bricks are commonly used to masonry heating furnace bottom. It should be noted that magnesium bricks are alkaline refractory materials, and clay bricks, high alumina bricks and silicon bricks at high temperatures have different degrees of reaction.
Magnesium-aluminum brick is to improve the thermal stability of magnesium bricks, by adding 5% ~ 10% Al2O3 in the ingredients and the formation of magnesium-aluminum spinel (MgO-Al2O3) combined with magnesium bricks, its refractoriness 2135 ℃, thermal shock stability and resistance to rapid cooling and rapid heating than magnesium bricks are better, the beginning of the loaded softening temperature is also improved, so it is a refractory material with excellent performance.
6.Silicon carbide refractory products
Silicon carbide refractory products are made of silicon carbide as raw material, adding binding agent (or no binding agent) after molding and firing. Its products are divided into three categories: (1) clay as a binding agent products; (2) to other mineral binding agent (ferrosilicon, quartz, etc.) products; (3) no binding agent (recrystallization) products.
Silicon carbide refractory material mechanical strength, abrasion resistance, resistance to rapid cold and heat, thermal conductivity (5 to 10 times larger than the general refractory materials), electrical conductivity and so on are very good, load softening point is high, deformation of the starting point of about 1600 ℃. The disadvantage is that the price is expensive, the use of temperature higher than 1300 ℃ is easy to be oxidized, and easy to be eroded by the alkaline slag, the more dense the texture of the silicon carbide material, the better its antioxidant properties. Silicon carbide refractory products are commonly used as electric furnace lining, muffle type furnace muffle wall, refractory electric heating plate and electric heating elements.
7.Graphite refractory products
Graphite refractory products are made of graphite as raw material and soft clay as binding agent. Its varieties are superior, first-class, second-class, third-class, refractoriness of 3000 ℃, the use of the temperature of 2000 ℃, the beginning of the load softening temperature of 1800 ~ 1900 ℃.
8.Aluminum oxide powder
The melting point of alumina powder is 2015°C. It is very stable in both oxidizing and strongly reducing atmospheres, and can be used in either type of atmosphere when the temperature is below 1900°C. Pure alumina has several crystalline structures at low temperatures, such as hexagonal (denoted by α), spinel (mixed oxides with the chemical formula RO-R2O3-type are known as spinels, denoted by β), and cubic (denoted by γ). However, all of these crystal types become high-temperature stable α-Al2O3 (corundum) when heated to temperatures above 1600°C, and this transformation is irreversible. Aluminum oxide powder can be used as refractory materials at temperatures below 1900°C, and is also a good thermal insulation material. Furnace construction workers are often wound with electric heating elements outside the furnace tube filled with 50 ~ 100mm thick Al2O3 powder is the reason. It is worth noting that, if the furnace atmosphere is carbon atmosphere, carbon particles are more likely to be deposited in the alumina powder, Ni-Cr resistance wire is very unfavorable, and even damaged. Alumina products are commonly used for sintering furnace refractory lining; also used as winding molybdenum or tungsten wire furnace tube or flame separator, operating in hydrogen or decomposition of ammonia atmosphere; can also be made into a boat, observation holes, crucibles, etc., alumina crucible is used to melt a variety of metals and oxides, its chemical stability is very high.
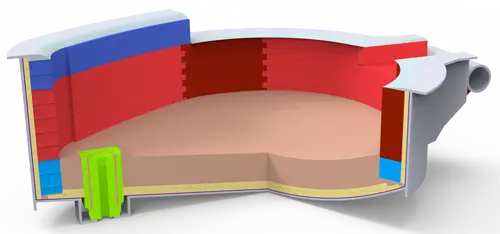