The development of induction furnaces is closely related to the progress of refractory technology. The design of large-scale industrial frequency crucible induction furnaces often starts with the selection of refractory materials and simulation tests of furnace linings. The increase in the capacity of groove induction furnaces, the expansion of the application range (from non-ferrous metal melting to ferrous metal melting), the insulation from cast iron to cast steel, and the increase in the power of a single induction body are all achieved after the development of melting groove refractory materials and the improvement of furnace construction technology.
In any case, the selection of furnace lining materials for induction furnaces is based on the utilization rate and economy of the furnace. Whether it is the crucible lining of a crucible furnace or the melting groove lining of a groove furnace, for the sake of electrical tight coupling, the thickness of the furnace lining is as thin as possible without affecting the service life.
In order to ensure the normal operation of the induction furnace, the following requirements are put forward for the refractory materials of the furnace lining:
1.Sufficient refractoriness
Materials with a refractoriness higher than 1580℃ are called refractory materials. The working temperature of the induction furnace lining is generally lower than the temperature of the molten metal. However, based on the requirements for the life of the lining, the accidental or frequent overheating of the molten pool and the molten groove must also be considered. It is often unsafe to use materials with low refractoriness and softening temperature in cast iron induction furnaces. As the lining material of the cast iron induction furnace, its refractoriness should be greater than 1650-1700℃, and the softening temperature should be higher than 1650℃.
2.Good thermal stability
Induction furnaces rely on electromagnetic induction to transfer energy. In order to ensure that the furnace has a high electrical efficiency, the thickness of the lining of the induction coil is limited, which makes the lining work under a large radial temperature gradient. In addition, during the operation of the furnace, due to the effects of charging, iron tapping, and even shutdown, the temperature of the lining is always changing. The lining often cracks due to uneven heating, which reduces the service life of the lining. Therefore, as a refractory material for an induction furnace, it should have excellent thermal stability.
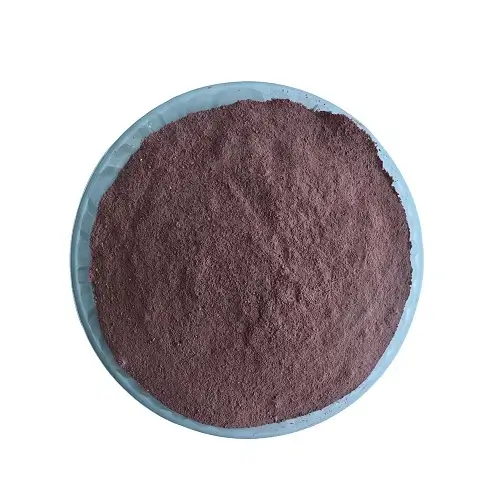
3.Good chemical stability
The chemical stability of the material is closely related to the life of the furnace lining. The furnace lining material should not be hydrolyzed and decomposed at low temperatures, should not be easy to decompose and reduce at high temperatures, should not easily form low-melting-point substances with the slag during the smelting process, should not easily react chemically with the molten metal and additives, and will not pollute the molten metal.
4.Small thermal expansion coefficient
As the temperature changes, the volume should be relatively stable, without drastic expansion and contraction.
5.Has higher mechanical properties
It must be able to withstand the impact of furnace charges at low temperatures; it must be able to withstand the net pressure of the molten metal and strong electromagnetic stirring when the metal is in a high-temperature molten state; and it must be wear-resistant and erosion-resistant under the long-term scouring of the molten metal.
6.Good insulation performance
The furnace lining must not conduct electricity at high temperatures, otherwise it will cause leakage and short circuit, resulting in serious accidents.
7.Good construction performance of the material
It should be easy to repair and have good sintering performance, and convenient to build the furnace and maintain.
Induction furnaces have very strict requirements on refractory materials. Almost no natural refractory material can meet the above requirements. This requires the selection of suitable refractory materials according to different use conditions. At the same time, natural mineral resources should be synthesized and reprocessed as necessary to make their performance meet the requirements of induction furnaces.