由于洁净钢及超低碳钢的发展以及节能降耗的要求,开发低碳耐火材料已成为必然趋势。目前,电弧炉各部位所用的含碳耐火材料如镁碳砖、铝碳质材料、Al2O3-MgO-C材料或其他含碳不定形材料,其主要的发展趋势是低碳化且长寿化。近年来,随着制备工艺的发展、新型结合剂的开发以及纳米碳在耐火材用技术的开发,使得含碳耐火材料向低碳化甚至无碳化方向发展变得有可能。
众所周知,含碳耐火材料中碳含量降低引起的主要问题是抗热震性及抗渣性下降。目前解决此问题的途径主要包括:
(1)通过改善结合碳的碳结构提高材料的抗热震性。传统含碳材料的结合剂多为煤焦油沥青或酚醛树脂,这些结合剂碳化以后的碳结构呈各向同性的玻璃态,所以使材料呈脆性,弹性模量高,对材料的热稳定性不利,且材料的高温强度也低。在煤焦油沥青或酚酸树脂中引入能石墨化的炭素前躯体或具有催化作用的氧化物后,这种改性结合剂在制品使用环境下能碳化成为石墨化碳,或原位形成纳米炭纤维,通过碳结构的改善及纳米炭纤维形成的增强作用来提高材料的抗热震性及高温强度。
(2)优化材料的基质结构。在碳含量大幅度降低的情况下,如何提高骨料颗粒与碳粒子的接触比率,即降低碳粒子的尺度并保证其高度分散,是改善低碳材料抗热震性及抗渣渗透性的重要措施之一。通过调整基质配料的粒度组成来控制气孔的尺寸、形状和分布,也会对材料的热导率产生明显影响。
(3)采用高效抗氧化剂。随着材料中碳含量的降低,对碳的防氧化保护尤为重要,所以采用合适的高效抗氧化剂也是十分必要的。
ABB型直流电弧炉炉底阳极所用的导电耐火材料决定了电弧炉底电极的寿命,要求其既要具有良好的导电性能,又要与炉壳绝缘,并保证绝对安全。最常用耐火材料是MgO-C砖。MgO-C质耐火材料要求具有如下特点:电酊率低、均匀且受温度的影响小,导热系数小,高温抗侵蚀性能好,高温力学性能和耐磨性好等。为满足性能要求,日本最早在该部位多采用高碳含量的MgO-C砖,碳含量最高可达25%。而国内多采用碳含量为18%的导电MgO-C砖。近年来,日本研究人员对电极用后残砖进行了分析,发现MgO-C砖的侵蚀及损毁主要是由于加热或冷却过程中砖缝的开裂引起的。由此提出,通过合适的残余膨胀来减小砖的收缩缝可有效改善电极MgO-C砖的耐用性。基于此,开发出新型电极MgO-C砖,这种镁碳砖无论在低温和高温下均保持了较低的电阻,具有较低的热膨胀和较高的残余膨胀(见图1)。这种新型砖在使用中性能非常稳定,极大的提高了ABB型炉底电极的使用寿命。
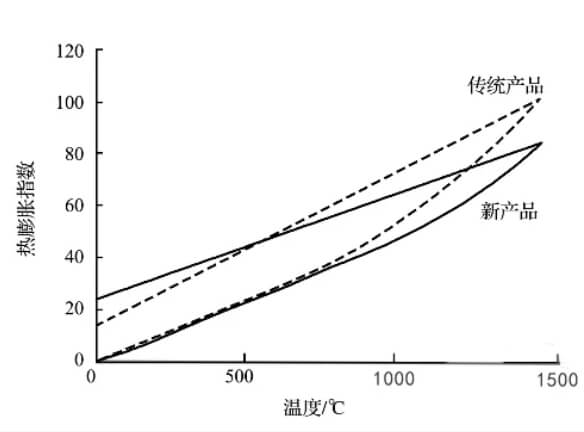
在电炉炉墙靠近电极的部位容易形成“热点”高温区域,会加速炉墙砖的侵蚀与损毁,造成局部熔损,这也是影响电炉寿命的关键部位。该部位使用的耐火材料主要有沥青结合高纯镁砖和镁碳砖,其中镁碳砖应用最广泛。有研究表明,采用高纯镁砂原料及添加金属粉促进致密化可以有效提高MgO-C砖的抗侵蚀性。日本的研究人员通过考察电炉内衬再砖的损毁因素,发现在高温下限制MgO-C砖中Mg蒸气的扩散速率可以降低砖的损毁速率。抗渣侵蚀性试验发现,随着MgO-C砖(1500℃热处理)显气孔率的升高,砖的侵蚀指数呈直线上升的态势。基于此,通过降低金属粉和碳含量,调整颗粒级配和生产工艺制备出致密结构MgO-C砖(HIDEN)。在热处理温度≤200℃时,HIDEN砖和传统MgO-C砖的显气孔率非常接近,但是经1000〜1500℃热处理后,HIDEN砖的显气孔率远远低于传统MgO-C砖的。HIDEN砖碳含量为8%,仅为传统MgO-C砖的一半,但是HIDEN砖具有优异的抗剥落性和抗侵蚀性。此外,在HIDEN砖工作面应用防脆化涂层,将砖应用于电弧炉侧壁工作衬,其使用寿命比传统MgO-C砖提高一倍,大大提高了电炉的生产效率。
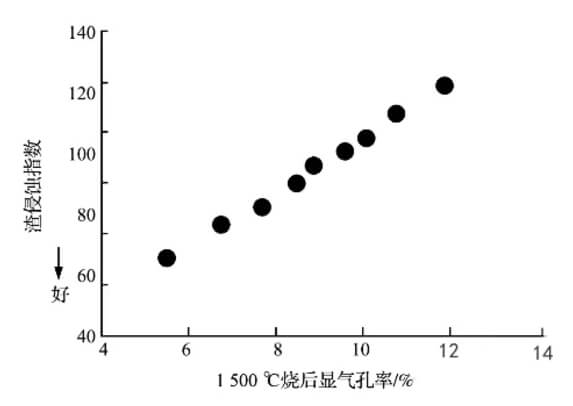
另外,鉴于浇注料已在钢包内衬得到广泛应用,但是用于电炉内衬时存在不易施工的问题,日本的研究人员开发出了与Al2O3-MgO浇注料成分相同的免烧Al2O3-MgO质砖,其基本性能列于表1,可替代传统的MgO-C砖用于电炉侧壁。与MgO-C砖相比,这种新型免烧砖具有较高的常温强度和较低的热导率,具有良好的节能效果。
由于水冷技术在电弧炉炉壁、炉盖上的广泛应用,渗水或水蒸汽都会引起MgO或镁钙质材料的水化,从而引起材料的损毁,油浸镁砖、沥青浸渍镁砖或镁钙质材料成为预防水化的可行措施。曰本开发的改性MgO砖(表2),具有优异的抗水化性,经高压釜(0.3MPa,3h)水化试验后,新型MgO砖的增重率只有0.1%,而传统MgO砖的增重率达到5.4%。在电炉永久衬应用这种新型MgO砖可有效避免炉衬修补时渗水或冷却系统漏水引起的水化现象,大大延长了炉衬的工作寿命,减少了永久衬的修补及更换次数,有效节约炼钢成本。
偏心底出钢口(EBT)由于水冷区域扩大、耐火材料费用降低并且使钢包中的卸渣量减少,因而应用逐渐增多。EBT出钢口一般采用EBT管,其外围用MgO-C砖砌筑,随着反复出钢的进行,出钢口被侵蚀且直径变大,需要更换维修,影响电炉的生产效率。如果通过增加EBT管壁的厚度来延长使用寿命,在早期会因为管内直径较小而导致出钢效率低下。为了控制出钢口EBT管的初始直径不变并且使出钢口有足够的耐用性,日本的研究人员通过试验对比三种致密砖的性能(见表3),发现与致密MgO-C砖相比,Al2O3-MgO-C砖不仅碳含量低,而且具有更好的耐磨性和抗侵蚀性,最终选取Al2O3-MgO-C材料为制备EBT管的主材料。所制备的EBT管初始孔径可以进一步扩大,应用于电炉出钢口后,出钢时间缩短,操作效率大幅提高。