电炉的炉底和堤坡共同构成了熔池,其耐火材料直接承受高温热负荷和熔渣的侵蚀,钢水冲刷、废钢机械撞击以及炉内高温下的氧化、还原操作,使熔渣渗透至炉底,导致炉底减薄。
超高功率电炉炉底用耐火材料
超高功率电炉炉底用耐火材料分绝热层用耐火材料、永久层用耐火材料和工作层用耐火材料。
1.绝热层用耐火材料
绝热层是炉底最下层,其作用是降低电炉的热损失,并保证降低熔池上下钢液的温度差。通常是在炉壳上先铺一层石棉板,再铺硅藻土粉,其上面平砌一层绝热砖。
2.永久层用耐火材料
永久层的作用是保证熔池的坚固性,防止漏钢。通常永久层用MgO为95%~96%的烧成镁砖砌筑,镁砖先用磨砖机修整,以保证砌砖的质量。镁砖的耐火度可达2000℃以上,其荷重软化开始温度,一般镁砖在1520~1600℃,而高纯镁砖可达1800℃。20~1000℃下镁砖的线膨胀率一般为1.2%~1.4%,并近似呈线性。镁砖的热导率较高,在耐火制品中仅次于炭砖和碳化硅砖,并随温度的升高而降低。镁砖的抗热震性较差,提高镁砖的纯度可适当提高抗热震性。镁砖在常温下的电导率很低,但在高温下如1500℃却不可忽视,若用于电炉炉底应引起注意。普通镁砖的烧成温度一般为1500~1650℃,高纯镁砖的烧成温度则高达1700~1900℃。该部位也可以采用镁炭砖砌筑,但比较少见。
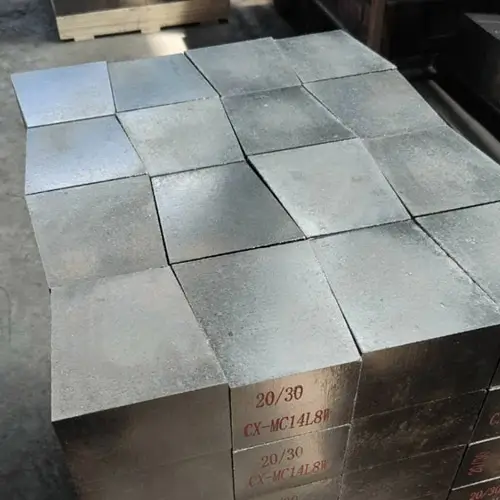
3.工作层用耐火材料
工作层用耐火材料直接接触钢水和炉渣,直接承受高温热负荷和熔渣的侵蚀,钢水的冲刷、废钢机械撞击以及炉内高温下的氧化、还原操作,使熔渣渗透到炉底,导致炉底减薄。而在非连续作业的时候,炉渣中的硅酸二钙吸收了大气中的水分而溃散脱落,降低材料的耐用性,影响其使用寿命。因此,该层耐火材料应具有:烧结性能良好,在保证烧结温度下快速烧结并形成一定的强度和一定厚度的烧结层,足以抵抗炉料的机械冲击。合适的膨胀性能,其膨胀和收缩既不会产生局部过大的裂纹以减少钢水和钢渣的侵入,也不会因为收缩产生的裂纹导致局部浮起,确保炉子能够连续作业。较大的自然堆积密度和烧后密度,既能避免因施工和烧结而造成的密度不均,又能有较高的抗钢水、钢揸渗透能力。抗钢水和钢猹侵蚀能力强,蚀损速率低、蚀损均匀,使用寿命长。炉底热面与新的炉底捣打料有较强的亲和能力,能确保修补效果。
普通功率电炉底耐火材料
普通功率电炉底通常有两种类型。
①打结炉底(或振动压缩炉底)。工作层使用镁砂,其结合剂为焦油、沥青,而制作无碳炉衬时,用卤水或水玻璃作结合剂。
②砖砌炉底。通常用沥青结合镁砖、无碳炉衬用卤水结合镁砖。
目前,高功率和超高功率电炉的工作层普遍采用镁质干式捣打料施工,该材料是以高铁高钙合成镁砂和电溶镁砂作骨料,以合成镁砂和电熔镁砂作细粉,临界粒度在5〜6mm,以合成镁砂中C2F(铁酸二钙)作助烧结剂,不添加任何结合剂,采用多级配料而成。通过强力捣打施工,保证施工后的密度,能够在适当的温度下烧结成坚实的整体,其寿命比以前的打结和砌砖方法要提高几倍。一般情况下使用干式捣打料一次性寿命可达到300炉以上,通过热修补可延长到500〜600炉,不但减少了停炉次数,而且吨钢耐火材料消耗明显降低。
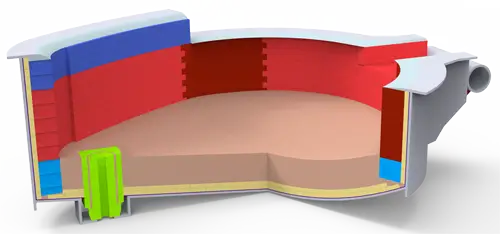